The Role of Insulation Jacketing in Pro-tection and Efficiency
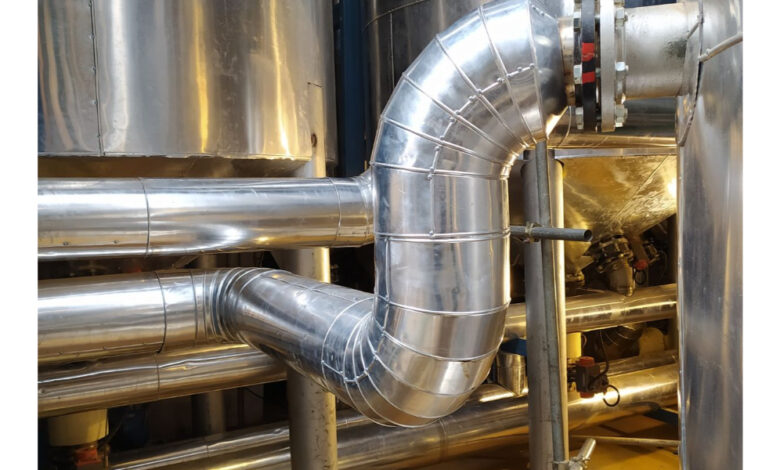
Insulation jacketing systems safeguard insulated pipes and ducts. Jacketings, also known as lagging or cladding, are intended and specified to keep insulating materials secure and prevent corrosion. Insulation jacketing is an outer coating that is wrapped over a tube or pipe insulation to protect it from moisture, wear, and mechanical damage. The jacket additionally supports the insulation while establishing the system’s emissivity and look. Insulation jacketing contributes significantly to insulation efficiency. Jacketed insulation systems differ from removable insulation blankets and pads, which are better suited for equipment that must be accessed often for maintenance or inspection.
There are numerous types of jacketing systems available, each constructed of a different material and with a varied thickness, providing a variety of physical qualities. This article discusses several factors to help you decide which type is best for your particular use.
-
Environmental Factors
The proper insulation jacketing system takes into account wear and tear from weather and overuse, as well as botched installation and incorrect maintenance. One rule of thumb for mitigating these concerns is to select the jacketing material based on the application. This means you should examine elements like:
- Relative humidity: How humid is the environment?
- Operating temperature: How hot or cool is the equipment when in use?
- Ambient temperature: What is the temperature of the operational environment?
However, effective jacketing also takes into account the environmental safety threats that workers face. This includes temperature, sound, and air quality.
-
Touch Temperature
Surface temperatures should never exceed the specified limit, as most people can tolerate temperatures at or below this level without being burned. Insulation regulates temperature, allowing less heat to escape while also providing freeze protection.
-
Acoustics
In order to avoid injury, noise levels in industrial areas must be kept under control. Insulation jacketing reduces noise by absorbing sound.
-
Clean air
Pollution in crowded workplaces should be kept to a minimum. Insulation jacketing lowers vapour and moisture in the air, which can contain contaminants.
Consider both physical environmental considerations (such as temperature and humidity) and the working environment, as they affect the individuals who operate near your equipment. With these factors in mind, it’s simple to choose the right insulation jacketing method.
-
Durability
System reliability and intended service life can also be considered when maintaining the system’s operational conditions as intended and required. Additional considerations may include:
- Future maintenance and repair frequency
- Abrasion and mechanical abuse during system inspections, maintenance, or repairs.
- Potential damage from ladders or foot activity – these can open up sealed seams and crack rigid insulations or compress fibrous insulations, reducing system performance.
- Corrosive environments
- The frequency of washdown
-
Safety
When choosing the best insulation jacketing system, always emphasize safety.
A high-quality jacket can provide an important barrier between workers and high-temperature components (the jacket does not reduce hot process temperatures, but the insulating material does). It should be noted that if a system is used outdoors, such as on a rooftop in bright sunshine, the black jacket material will be hotter to the touch than the white system. Jackets also protect against humidity and moisture, thereby improving thermal performance and preventing mould growth or corrosion beneath insulation (CUI). Metal jacketing, such as stainless steel or aluminium, is often hemmed to prevent injury from sharp edges.